Plan de Mantenimiento Ejemplo: Cómo mantener tus equipos en óptimas condiciones
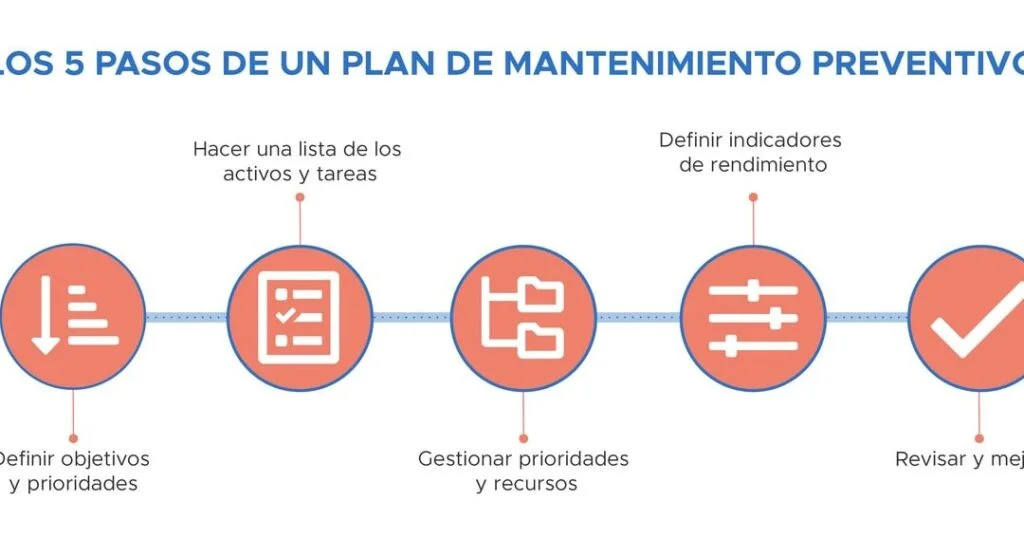
El mantenimiento adecuado de los equipos es esencial para garantizar su correcto funcionamiento y prolongar su vida útil. Un plan de mantenimiento bien estructurado y ejecutado regularmente puede ayudar a evitar costosos fallos y reducir el tiempo de inactividad. En este artículo, presentaremos un ejemplo detallado de un plan de mantenimiento para ilustrar cómo se puede implementar en cualquier industria.
Objetivos del Plan de Mantenimiento
Antes de comenzar a diseñar un plan de mantenimiento, es importante establecer los objetivos claros que se desean alcanzar. Estos pueden variar según el tipo de equipo y la industria, pero algunos objetivos comunes incluyen:
- Mantener la seguridad: Garantizar que los equipos estén en condiciones seguras de operación para prevenir accidentes.
- Maximizar la eficiencia: Optimizar el rendimiento de los equipos para minimizar el consumo de energía y los costos operativos.
- Prolongar la vida útil: Realizar un mantenimiento preventivo regular para prevenir averías y prolongar la vida útil de los equipos.
- Reducir el tiempo de inactividad: Minimizar el tiempo de inactividad no planificado debido a fallas y reparaciones.
Ejemplo de Plan de Mantenimiento
Paso 1: Identificación de los equipos
El primer paso en la creación de un plan de mantenimiento es identificar todos los equipos que se deben incluir en el programa. Por ejemplo, en una planta de manufactura, esto puede incluir maquinaria, sistemas de climatización, sistemas eléctricos, entre otros.
Ejemplo: En una fábrica de alimentos, los equipos a incluir en el plan de mantenimiento pueden ser: líneas de producción, hornos industriales, equipos de refrigeración, sistemas de transporte, entre otros.
Paso 2: Evaluación de las necesidades de mantenimiento
Una vez identificados los equipos, es necesario evaluar las necesidades de mantenimiento específicas de cada uno. Esto implica determinar la frecuencia y los tipos de mantenimiento necesarios, como inspecciones regulares, lubricación, calibración, reparaciones, etc.
Ejemplo: Para los equipos de la planta de alimentos mencionada anteriormente, se pueden establecer las siguientes necesidades de mantenimiento: las líneas de producción requieren inspección diaria, los hornos industriales necesitan limpieza y calibración mensual, los equipos de refrigeración deben ser revisados trimestralmente, y los sistemas de transporte necesitan lubricación semanal.
Paso 3: Creación de un calendario de mantenimiento
Una vez que se han evaluado las necesidades de mantenimiento, es importante establecer un calendario de mantenimiento para asegurarse de que todas las tareas se realicen de manera oportuna. Esto implica asignar fechas específicas para cada actividad de mantenimiento y asignar responsabilidades a los miembros del equipo encargados de llevar a cabo las tareas.
Ejemplo: En el caso de la fábrica de alimentos, se puede establecer un calendario de mantenimiento de la siguiente manera:
- Líneas de producción: Inspección diaria por el supervisor de producción.
- Hornos industriales: Limpieza y calibración mensual realizada por el técnico de mantenimiento.
- Equipos de refrigeración: Revisión trimestral realizada por el técnico de refrigeración.
- Sistemas de transporte: Lubricación semanal realizada por el operador de la línea de producción.
Paso 4: Registro y seguimiento del mantenimiento
Es fundamental llevar un registro detallado de todas las actividades de mantenimiento realizadas. Esto permite realizar un seguimiento de las tareas completadas, identificar patrones de fallas y evaluar la efectividad del plan de mantenimiento en general.
Ejemplo: Para la fábrica de alimentos, se puede utilizar una hoja de cálculo o un software de gestión de mantenimiento para registrar y realizar un seguimiento de todas las actividades de mantenimiento. La información registrada puede incluir la fecha de la actividad, la descripción de la tarea realizada, las piezas reemplazadas (si corresponde), el tiempo dedicado a la tarea, entre otros detalles relevantes.
Un plan de mantenimiento bien estructurado y ejecutado regularmente es esencial para garantizar la operación segura y eficiente de los equipos. El ejemplo proporcionado en este artículo ilustra los pasos clave para desarrollar un plan de mantenimiento efectivo. Recuerda adaptar este ejemplo a las necesidades específicas de tu industria y equipos para obtener los mejores resultados.
Entradas Relacionadas